OMI Jofu (Ramie Textiles)
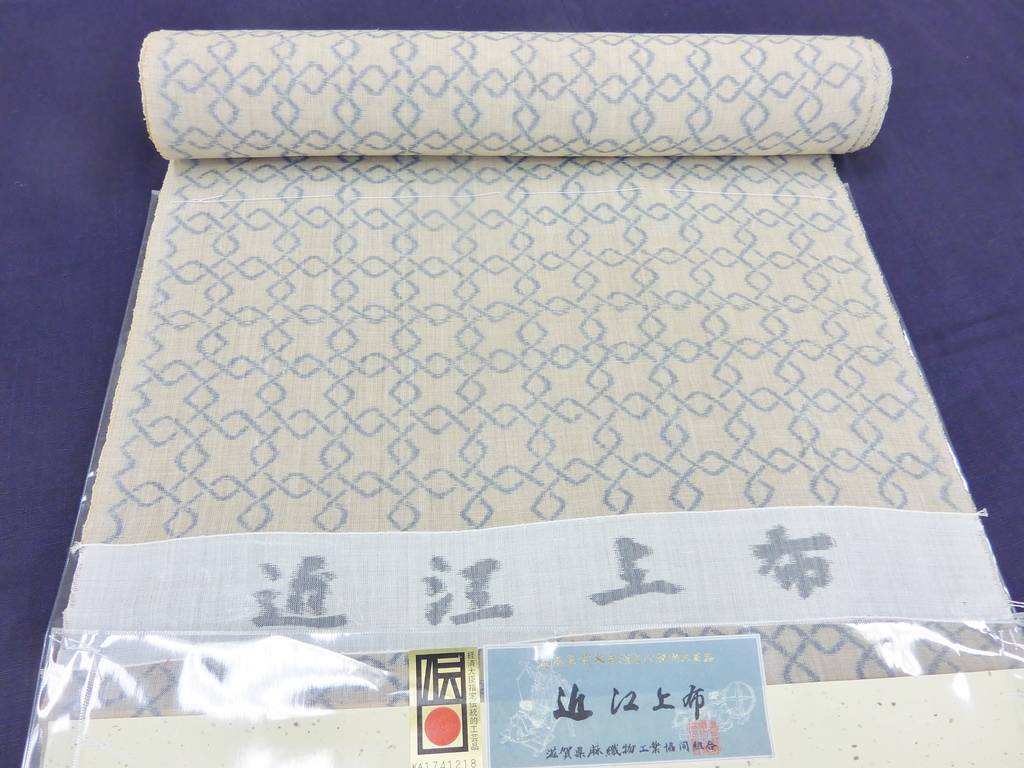
In the Omi area during the Kamakura period (1185-1333), production of woven ramie cloth was fostered by the well-known entrepreneurial spirit of Omi tradesmen, the hot local climate and a plentiful supply of water from the Aichi River.
The craft flourished during the Edo period (1600-1868) with encouragement from the Hikone clan, which ruled the area around Hikone on the southern shores of Lake Biwa, and it became a well-established local industry. From that time, great improvements were made in dyeing techniques, giving rise to the superb ikat patterns characteristic of Omi Jofu.
The ikat is either in the weft alone or in both the warp and weft. Weft threads are bound before being dyed using a stencil for the weft ikat cloths. In the case of the warp and weft ikats, both sets of threads are dyed by applying dye to the bound threads. The positions of the warp and weft threads are adjusted as the cloth is woven to produce one of the top fabrics across the entire craft. Ramie is a very comfortable, cool fabric that absorbs moisture. These days, the fabric is generally used for traditional garments, but is also found in jackets.
Feature
Omi Jofu fabrics can be divided into yokoito-gasuri and tateyoko heiyo-gasuri. In yokoito-gasuri, the cross thread is “feather-winded” and paper stencil-printed (katagami nassen). In tateyoko heiyo-gasuri “comb pressing” (kushi oshi nassen) is performed on both yarns, and garments are woven while aligning warp and weft. This makes for premium quality items. Hemp, thanks to its moisture-absorbing properties, feels cool, refreshing and comfortable when worn.
How to make
Resisted yarn dyeing is performed on yarn that has been spun very thinly. The two main dyeing techniques used are “comb pressing” (kushi oshi nassen) and “paper stenciling” (katagami nassen). The woven fabric is then subjected to a unique Omi shrinkage process called “graining” and carefully finished.