NANIWA Hon Zome (Dyeing)
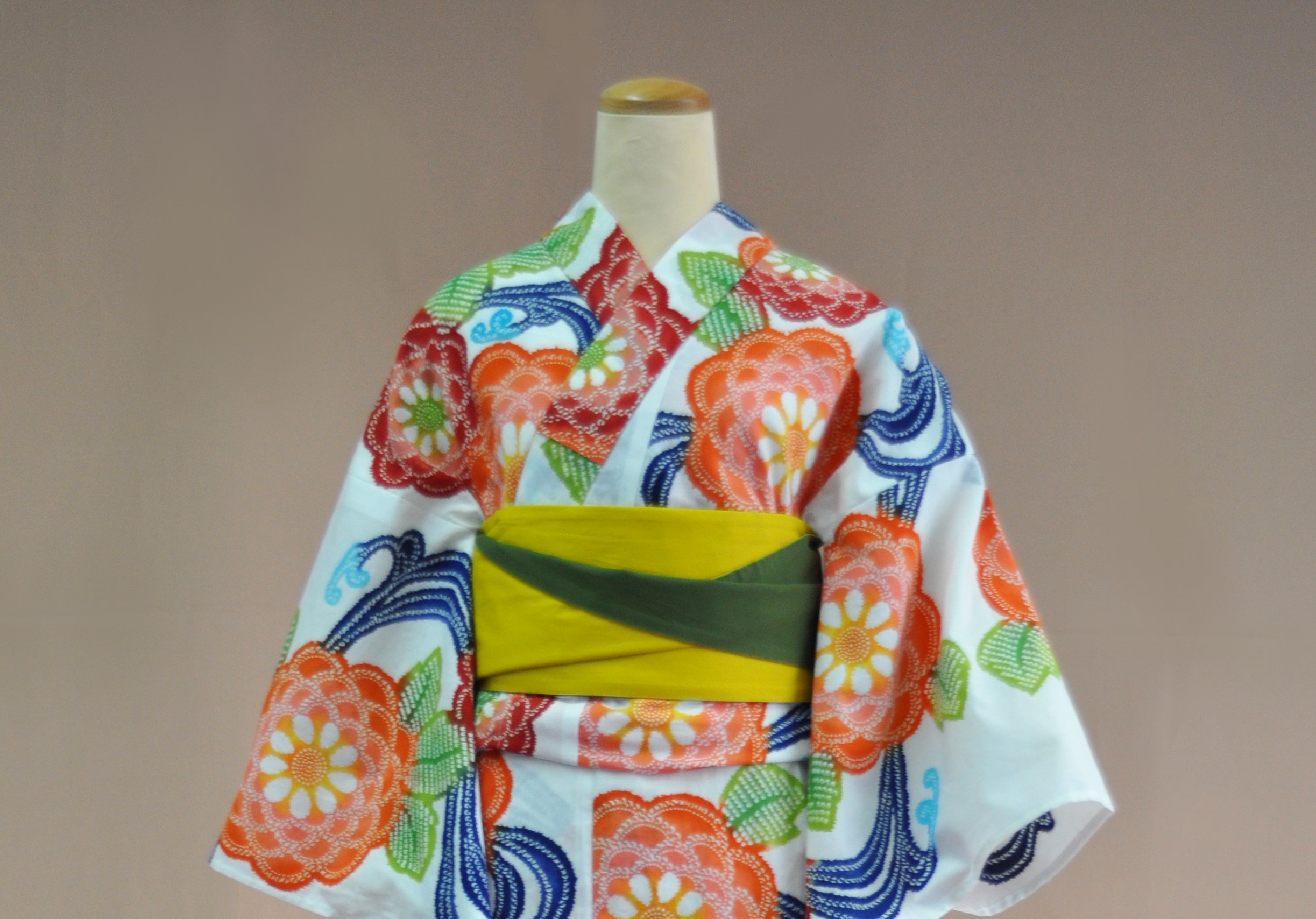
Naniwa Honzome is an original Japanese type of dyeing that was developed during the Meiji era in Osaka to mass produce patterned handkerchiefs. It’s also commonly called chusen, or injection dyeing, and the threads are dyed to their core from both the front and back, producing a product with great texture. Japanese yukatas (summer kimonos) dyed in this method were well-received and became common throughout the country. Aside from handkerchiefs and yukatas, today it is used to create other daily use items, including Hawaiian shirts, coasters and sun parasols.
Feature
Features Since the Edo era, Osaka was the home of handkerchief manufacturing. In the year Meiji 20 (1887) a dyeing method that involved layering fabric covered in dye-proof paste and applying dye over the top was born. The Meiji era artisans of the time built on this innovation, using techniques called sashi wake or bokashi (blurring) to create dyes of myriad colors, and another dyeing technique called hoso kawa. This allowed them to polish techniques that further brought out traditional Japanese textures only possibly through hand dyeing. Today, these styles are collectively known as Naniwa Honzome Hand Dyeing.
How to make
Artisans that used the dye-proof paste were known as itaba, and those that implemented the array of colors were known as tsubondo. Itaba artisans manipulated the mold for their dyes and folded the dye-proof paste into the mold to create different dyed patterns. Next, the tsubondo would take a bundle of fabric with intricately layered dye-proof paste applied and actually dye it. The patterns created outside of the dye-proof paste are filled in with brilliant color using sashi wake or bokashi (blurring) techniques. The dyed fabric is then cleaned of any extra paste or dye and dried in the sun before becoming the completed handkerchief.